Jetex
Motor Manufacturers Checklist
Manufacturer
Jetex
(Wilmot Mansour,
UK)
|
Distributors
American
Telasco (NY), sole US
distributor
|
Engine
Model Designations
Jetex Atom 35
(introduced Sep
1953)
Jetex 50
("Standard" May 1949-1954; machined
aluminum alloy, ribbed
casing)
Jetex 50
("Export"; pressed aluminum alloy;
rounded ends)
Jetex 50B
(pressed steel; as 50 "Export" but a bit
longer; introduced Sep
1953)
Jetex Hell-Cat
50 (? This
designation may have only been used
later, for Sebel
motors)
Jetex 100
(1948; 3 coil
springs)
Jetex Jetmaster
(Jun 1952; "100"
size)
Jetex
PAA-Loader 150
Jetex 200
(1948; 5 coil
springs)
Jetex 350
(1948; 5 coils prings, later called the
"Spacemaster 600A")
Jetex Scorpion
600 (introduced Sep
1953)
Jetex
Spacemaster 600A (same as
350)
|
Jetex (Sebel, UK)
|
American Telasco (NY), sole US distributor
originally
Aristo-Craft (NY) ???
|
Jetex Atom
35 ???
Jetex
50B ???
Jetex
50C
Jetex Rocket
HT 50 ???
Jetex Hell-Cat
50 ???
Jetex
PAA-Loader 150 ???
Jetex Scorpion
600 ???
Jetex
Spacemaster 600A
|
South Shore
Metal Products, Inc. (No. Amityville,
NY)
|
Berkeley
Models
|
Psst
50
Psst Double
50
|
Powermax (UK)
|
Powermax (UK)
Davis Model Products
(US)
PVHC (US)
Peck Polymers (US)
Dare Products (US)
|
Jet-X
35
Jet-X 50
(1985)
Jet-X
50C
Jet-X
50Z
Jet-X
100
Jet-X
100Z
Jet-X 100Z Mark
II
|
"Official
Nomenclature"
There are some
"official" terms used to describe the various
Jetex motor parts and components. Here are the
basics, based on a Jetex 150-PAA Loader
engine.
1: Main case (in larger rockets, called
the thrust chamber
2: Spacer (a balsa plug, used when single
fuel pellets are burned)
3: Insulator disc (used between the
single fuel pellet and the
spacer)
4: Pellet (propellant)
5: Jet wick (fuse)
5A: Wire gauze disk (serves as a burn
rate catalyst)
6: Flame shield (protects end cap and
nozzle from propellant burn
heat)
7: Cap sealing washer (this is the
over-pressure safety seal)
8: Spring safety clip (which keeps the
case closed, unless pressure gets too
high)
9: End cap assembly (in larger rockets,
called the "aft closure
assembly")
10: Jet nozzle (only the exhaust hole;
this is not a separate part)
11: Jet wick, lead in (represents the
exterior part of the wick/fuse)
Jetex Motor Specifications
(Comparative)
Data posted in green
is from original factory packaging and
instruction sheets
Data in black is from
our own recent measurements (bold) or other
"non-official" sources
Figures in red
indicate extrapolations, and must be regarded
as approximations at best
Engine
Models
|
Thrust
(avg, oz)
[gm]
|
Duration
(sec/
pellet)
|
Duration
(max, sec)
|
Weight
(loaded, oz)
[gm]
|
Weight
(dry, oz)
[gm]
|
Propellant
Wt (min, oz)
[gm]
|
Propellant Wt (max,
oz)
[gm]
|
Total
Impulse (oz-sec)
[N]
|
Propellant
Mass
Fraction²
|
Jetex Atom
35
|
0.4-0.5
[11.3-14.2]
|
7-8
|
7-8
|
0.25
[7.1]
|
0.156
[4.42]
|
0.094
[2.66]
|
0.094
[2.66]
|
2.8-4.0
[0.78-1.11]
|
0.62
|
Jetex 50
(Standard)
|
0.50-0.63
[14-18]
|
14-15
|
14-15
|
0.36
[10.2]
|
0.25
[7.1]
|
0.11
[3.12]
|
0.11
[3.12]
|
7.0-9.5
[1.95-2.64]
|
0.69
|
Jetex 50
(Export)
|
0.50-0.63
[14-18]
|
10-12
|
10-12
|
0.30
[8.4]
|
0.19
[5.3]
|
0.11
[3.12]
|
0.11
[3.12]
|
5.0-7.6
[1.39-2.10]
|
0.63
|
Jetex
50B
|
0.50-0.63
[14-18]
|
10-12
|
10-12
|
0.33
[9.3]
|
0.22
[6.2]
|
0.11
[3.12]
|
0.11
[3.12]
|
5.0-7.6
[1.39-2.10]
|
0.67
|
Jetex 50C
|
0.75-0.87
[21-25]
|
7
|
14-15
|
0.5
[14.1]
|
0.31
[8.9]
|
0.09
[2.66]
|
0.18
[5.32]
|
|
|
Jetex
Rocket HT-50
|
3.5-5.0
[99-142]
|
4-5
|
|
0.5
[14.2]
|
0.375
[10.6]
|
|
|
|
|
Jetex
Hell-Cat 50
|
0.6
[17]
|
7
|
15
|
0.4
[11.3]
|
0.2
[5.7]
|
|
|
|
|
Jetex
100
|
1.0-1.3
[28.4-36.9]
|
14-15
|
14-15
|
0.875
[25]
|
0.63
[17.7]
|
0.25
[7.09]
|
0.25
[7.09]
|
14.0-19.5
[3.89-5.42]
|
0.72
|
Jetex Jetmaster
|
1.75-1.88
[50-53]
|
12-15
|
12-15
|
0.94
[26.6]
|
0.69
[19.5]
|
0.25
[7.09]
|
0.25
[7.09]
|
21.0-28.2
[5.84-7.84]
|
0.73
|
Jetex 150
PAA-Loader
|
1.75-2.0
|
7
|
18-20
|
|
0.9375
|
|
|
|
|
Jetex
200
|
2.75-3.25
[77.9-92.1]
|
12
|
24
(2)
|
1.56
[44.30] (1)
1.88
[53.16] (2)
|
1.25
[35.4]
|
0.31
[8.86]
|
0.62
[17.72]
|
33.0-78.0
[9.17-21.68]
|
0.66
|
Jetex 350
(also called Spacemaster
600A)
|
3.5-4.0
[99.2-113.4]
|
12
|
12
(1)
24
(2)
36
(3)
|
2.75
[78.0] (1)
3.13
[88.7]
(2)
3.50
[99.2] (3)
|
2.37
[67.3]
|
0.375
[10.6] (1)
|
0.75
[21.3]
(2)
1.125
[31.9] (3)
|
42-48
[11.7-13.3] (1)
84-96
[23.3-26.7] (2)
112-144
[31.1-40.0] (3)
|
0.68
|
Jetex
Scorpion 600
|
4.0-5.5
[113.4-155.9]
|
8-10
|
12-16
|
2.0
[56.7]
|
1.625
[46.1]
|
0.375
[10.6]
|
0.375
[10.6]
|
32.0-66.0
[8.9-18.3]
|
|
|
|
|
|
|
|
|
|
|
|
Jet-X Atom
35 (Powermax)
|
2.5
[70.9]
|
|
|
|
0.106
[3.00]
|
|
|
|
|
Jet-X 50
(Powermax)
|
1.2
[40.8]
|
7
|
|
0.353 [10.00]
(3)
|
0.282
[8.00]
|
|
|
8.4
[2.3]
|
0.80
|
Jet-X 50C
(Powermax)
|
|
|
|
|
|
|
|
|
|
Jet-X 50Z
(Powermax)
|
1.6
[45.4]
|
7
|
|
0.423
[12.00]
(3)
|
0.353
[10.00]
|
|
|
11.2
[3.11]
|
0.83
|
Jet-X 100
(Powermax)
|
|
|
|
|
|
|
|
|
|
Jet-X 100Z
(Powermax)
|
2.0
[56.7]
2.8
[79.3]
|
7
|
15-26
|
0.846
[24.0]
(3)
|
0.67
[19.0]
0.705
[20.00]
|
0.088
[2.5]
|
0.35
[10]
|
19.6
[5.45]
|
0.83
|
Jet-X
100Z
Mk II
(Powermax)
|
2.8
[79.3]
|
7
|
|
0.776
[22.0]
(3)
|
0.635
[18.00]
|
|
|
19.6
[5.45]
|
0.82
|
|
|
|
|
|
|
|
|
|
|
Psst
50
|
|
|
|
|
|
|
|
|
|
Psst Double
50
|
|
|
|
|
|
|
|
|
|
1: AT = augmenter
tube
2: Dry weight / loaded
weight; a comparison of
efficiency
Lab Reports
A rather intensive
series of scientific tests were made of the
Jetex engine series in 1953-1954, by Ron
Warring for Aeromodeller magazine. This
is the best performance information we've yet
found. The following remarks are based upon
articles titled “Engine Analysis No. 15
(New Series), by Ron Warring, in
Aeromodeller (Nov & Dec 1953, and
Jan 1954), to which we give credit.
Click here to view
"Engine Analysis No.
15 (New Series)"
Augmenter Tubes
The makers of Jetex
originally offered two sizes of "augmenter
tubes," which were formed from thin aluminum
sheet; the forward end is bell-mouthed and
considerably larger in diameter than the Jetex
engine (one tube size is for the two 50
engines, the other for the 150 and 600), and
the edge of the bell is placed about even with
the rear of the engine
case.
When the jet is
operating, cool air is drawn into the tube
mouth and is expelled at the tail of the model
along with the hot gases. This air not only
cools the gases but contributes to thrust.
Figures show that the augmenter will increase
thrust from 20 to 30 per
cent.
Ignition is not
difficult with these tubes in place; they
prevent the sparkling fuse from burning the
model interior, too. To work successfully,
plenty of air must be able to reach the forward
end of the augmenter. This accessory is
normally used only inside closed fuselages, as
it would have quite a lot of air drag on an
open-fuselage Jetex-engine
installation.
...
...
Jetex 50 augmenter tube kit [click B&W
images to see full-size color
illustrations]
Jetex Jetmaster augmenter tube kit, with
the extension tube made in two parts that clip
together [click image to see full-size color
illustration]
...
Jetex PAA-Loader 150 augmenter tube [click
images to see full-size color
illustrations]
Other
Jetex Accessories
Among the curious and
unusual Jetex accessories we've seen is this Dempster Turb-O-Prop, a Techni-Bilt Product from the Dempster Co. in Kansas City. Billed as "the first practical replacement for rubber-band power", it was spun by the exhaust gases from the 50-size pellets burnt in the unit in front of the propellor. One of these sold on eBay in November 2002 for $170.50. Does
anyone know if it
works?
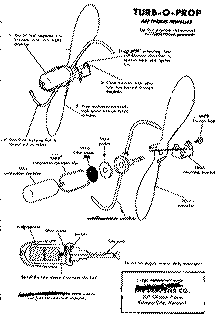
[Click image to see
full-size drawing]
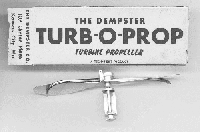
[Click image to see
full-size color
photo]
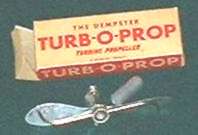
Rapiers and Other Micro
Rockets
There are several
other kinds of small rockets on the market
today, but none has the features of the
Jetex.
Most notable of these
is the Rapier, similar
to Estes motors in configuration, with
Jetex-like performance. Graham Knight
reports:
" ... they just look
like an Estes rocket, cardboard tube with a
nozzle at one end. Performance, L1 is less
power than a Jetex 50, I guess about 70%, L2 is
a bit more, maybe 110%. I haven't seen an L4
yet but hear it is more power than L2 and burns
longer. Burn time for L1 & L2 is around
20-25 secs. Performance does vary a bit from
motor to motor. If you like Jetex you'll love
these!"
...
We've also heard that
there are no mounting provisions accompanying
the Rapiers. However, the instruction sheet
suggests several options, among them the use of
Velcro; gluing the motor to the model; metal
clips; and slipping the motor into a pre-formed
paper tube attached to the
airplane.
"The units are about
the same diameter as schoolroom chalk, 1-1/2"
long for the small units, and 2 inches for the
larger size. Each motor consists of a
cardboard outer casing (about 1/16" wall
thickness) filled with molded propellant.
Unlike the old Jetex motors, Rapiers have no
nozzle. However, like Jetex they are ignited
via a separate fuse, which fits into a hole
molded in the "output end" of each
motor."
The Rapier motors are
made by:
Dr.-Ing. Jan
Zigmund
Jirankova
2281
530 02
Pardubice
CZECH
REPUBLIC
We
received this technical information from Dr.
Zigmund:
Model jet propulsion
units Rapier are designed for recreation and
sport flying to power balsa or paper aircraft
models. The units are manufactured of a card
tube that is filled with pyrotechnic
propellant. On one end the unit is closed with
a refractory nozzle, on the other end with a
refractory cover. Provided the directions for
use are followed, the construction of the units
provides the user with a sufficient safety when
handling the unit. No dangerous fragments of
material fly away from the card tube on a
prospective rupture of a unit. If a rupture of
a unit occurs, the wall of the card burning
chamber usually burns through and the
propellant burns up quietly. Thickness of the
tube is chosen to allow the tube surface to be
heated approximately only to 150°C after
the burn up of the propellant. Interior of the
card tube is charred in so far that its
prospective filling with a home made propellant
leads to a crush of the
chamber.
Model jet
propulsion units Rapier are marked by a low
thrust and long burning time. Dependent on
chemical composition of the propellant it is
possible to obtain burning time of about 20
seconds and thrust ~50 mN (5ponds) at Rapier
L -1 units, and burning time of about 25
seconds and thrust ~75 mN with Rapier L -2
units. L - 1 and L - 2 units are designed to
power chuck - gliders and aircraft models
with wing span 250 - 400 mm and weight up to
25 g. I recommend that the weight of models
should be from 2x up to 3x of thrust of jet
unit in ponds (see performance of jet unit at
the side of a box). The achieved flight times
are 40 - 300 seconds.
Model jet
propulsion units Rapier are analogous to
widely spread JET-X motors that could have
been used repeatedly. Jet units Rapier are
designed, contrary to JET-X, for one flight
only. The possibility of repeated utilization
has been replaced by more comfortable
handling and safer function. The unit is
simply inserted by its front part into the
container fitted to the aircraft model. With
this arrangement the unit is cooled during
the flight and after burnout it is easy to
remove from the container without any danger
of burning. Burning chamber is thrown off
after burnout.
My aim is to offer
the modellers romance and excitement of
flight of jet unit propelled model again. I
would like to let the modellers have a
possibility to experiment and find their own
way to the best construction of an aircraft
model.
My intention is to
produce jet units of L line (series) i.e. for
chuck gliders and aircraft models. The units
will be packed in green boxes and marked with
L letter.
According to
customers’s interest I would like to
produce also modellers rocket motors in
future. They will be packed in red boxes and
marked with R letter to avoid mistaking them
for L units.
I would like to
express my thanks to all modellers and
friends who encouraged me to forward with
development of Rapiers.
|
Rapier
L-1
|
Rapier
L-2
|
Rapier
L-4*
|
Length (mm)
|
40
|
50
|
50-60
|
OD (mm)
|
10
|
11
|
14.6
|
ID (mm)
|
6.5
|
7.5
|
10
|
Weight, loaded
(g)
|
5.0
|
7.3
|
11.6
|
Weight, dry
(g)
|
2.1
|
2.8
|
5.0
|
Weight, propellant
(g)
|
2.9
|
4.5
|
6.5
|
Propellant mass fraction
(Wp/Wl)
|
0.58
|
0.62
|
0.56
|
Duration
(sec)
|
~20
|
~20
|
14-20
|
Thrust (avg,
mN)
|
~50
|
~75
|
~150-170
|
Total impulse (total,
Ns)
|
~1
|
~1.75
|
~2.5
|
* in
development
Dr. Zigmund's letter
also refers to the Czech certification of the
motors and fuse (Decision No. 214 - 99 - 0167/V
06317 was rendered on August 12, 1999 by the
Authorized State Testing Laboratory No. 214
VVUÚ a.s., Pikartská 7 716 07
Ostrava - Radvanice, Czech Republic: to
certify "Model jet propulsion units RAPIER"
At the same time decision No. 214 - 99 - 0168/V
06318 was rendered to certify "Fuse type 07"
designed for Rapier
units.)
Thank you, Dr.
Zigmund. We're now converting his Standard
Units to a more familiar British Units, for
ready comparison to Jetex
specifications.
There are several
other kinds of small rockets on the market
today, but none have the features of the
Jetex. All of the other reloadables are
bigger--much bigger. And all the rest of the
small rockets are really high-impulse boosters,
offering nothing in the way of sustained
power.
This illustration
shows both the Apogee 1/4-A and the Estes B
sized conventional (high thrust, short
duration) model rocket engines. The Apogee
1/4-A motors, propelled by black powder, are
quite light and effective when a very short
burn time can be applied. The B size motors,
also with black powder, are the next step up in
physical size and performance. These two
motors represent the main alternatives to Jetex
propulsion in micro rocket sizes. Great for
their own special (ballistic) applications,
neither work well for freeflight
aeroplanes.

[click image to see
full-size graphic]
This graph shows the
thrust curves for several common 1/2-A through
D size conventional small rocket motors. Note
the thrust is at best one or two seconds.
1/2-A motors produce a total impulse of about
0.28 pound-seconds (1.25 Newton-seconds). The
larger D motors produce a total impulse of
about 4.5 lb-sec (20 N-sec), and reach nearly 7
pounds at peak thrust. The largest Jetex
engines produce perhaps 6 ounces of thrust, for
perhaps 15 seconds.
NAR
Standard Model Rocket
Classifications
Larger rocket motors
are customarily rated by their thrust and burn
duration, the product of which is called their
"total impulse," and is often rated in
pound-seconds. This refers to the equivalent
amount of forward thrust the motor produces, in
pounds, if all the propellant burned for one
second. Thus a motor with 500 lb-sec total
impulse might burn at 100 lbs thrust for 5
seconds, or 1 lb thrust for 500 seconds. The
important thing to remember is that "total
impulse" refers to total thrust yield over the
burning duration; this is not the same as
average thrust (unless the motor happens to
burn exactly one second).
Total impulse is the
starting point for determining a rocket
propellant's efficiency, which is called
"specific impulse," or Isp. Specific impulse
is the total impulse (power generated) of the
propellant divided by its weight. This number
is measured in "seconds."
Thus, a motor which
produces 500 lbs thrust for 1 second has 500
lb-sec total impulse. If this motor burns 5
lbs of propellant to produce this thrust,
then
500 lb-sec / 5 lb =
100 lb-sec/lb, or 100 sec
Accordingly, 100 is the
Isp of the propellant burned. Black powder
produces an Isp of less than 100, while advanced
composite (polymer-fuel) propellants produce Isp
ratings of nearly 300. The higher the Isp, the
higher the thrust x time per pound
burned.
Model rocket motors
have long been classified by a standard adopted
by the (US) National Association of Rocketry.
These apparently arbitrary classifications have
proven useful for both standardization of motor
sizes and performance, and for safety
classifications by
legislators.
For many years the
only model rockets produced were of the A, B,
C, and D classifications, which produce less
than 20 newton-seconds (or about 4.5
lb-seconds) of total impulse. More recently,
smaller and larger motors have reached the
market, including the new Micro-Maxx (by Quest)
which is rated at 1/8A, and produces less than
1 ounce-second of total impulse. The largest
commercial "model" rockets today go into the M
and N classes, and produce hundreds of
pound-seconds of total
impulse.
Jetex motors fall
within the A through D classes shown in the
table below, based upon their total impulse.
Jetex 50 is an A class motor, for instance,
producing about 0.5 ounce thrust for about 15
seconds, or a total of 7.5 ounce-seconds total
impulse. The "big" Jetex 600A Spacemaster
produces over 200 ounce-seconds of total
impulse.
Note that the NAR
motor classifications are based only upon the
total propellant impulse, as measured in
newton-seconds. A newton-second is the thrust
force of one newton operating over a one second
period of time. (1 lb = 4.448 newtons; 1 oz =
0.278 n; 1 gm = 0.0098
n)
NAR Standard Model
Rocket
Classifications
Rocket Motor
Classification
|
Total Impulse
(newton-seconds)
|
Total Impulse (gram-seconds,
±)
|
Total Impulse (oz-seconds,
±)
|
1/8A
|
0--0.31
|
0--32
|
0--1.125
|
1/4A
|
0.32--0.63
|
32--64
|
1.125--2.25
|
1/2A
|
0.64--1.25
|
64--128
|
2.25--4.5
|
A
|
1.26--2.50
|
128--256
|
4.5--9.0
|
B
|
2.51--5.00
|
256--512
|
9--18
|
C
|
5.01--10.00
|
512--1024
|
18--36
|
D
|
10.00--20.00
|
1024--2048
|
36-72
|
|