These
articles are currently held here in the
archive:
Engine
Analysis No. 15 (New Series)
Part 1: The Jetex 350, 200 &
Scorpion (Aeromodeller, Nov
1953)
Ron Warring
To include tests on Jetex motors in a
series of engine tests may seem a little
strange but the rocket motor is just as truly
an "engine" as an internal combustion engine
and, furthermore, the Jetex is the only
practical form of small scale jet unit at
present suited to all types of free flight
models. Its only rivals in this respect have
been the compressed C02 jet "motor" (a capsule
of compressed C02 suitably pierced to allow the
compressed gas to escape at high velocity), and
the more recent ducted fan. The former had
many limitations and found only temporary favor
The latter is, of course, merely another way of
producing "propeller thrust" from a
conventional motor and not in the same category
as a pure jet engine.
The Jetex motor, of course, delivers
thrust direct, unlike the reciprocating engine
which turns a shaft on which is mounted a
suitable thrust-producer, e.g. a propeller or
fan. In computing the respective performances
the direct thrust of the jet engine is
measured, whereas in the case of the internal
combustion engine the power developed at the
shaft is determined, and this varies with the
load applied to the shaft (i.e. the size of the
propeller). The resulting thrust, in the
latter case, is a function of the efficiency of
the propeller as well as the power of the
engine. Due to inevitable propeller losses, in
other words, the effective power of the engine
(as expressed in terms of the useful thrust
provided) is lower than the measured or brake
horse power determined on test.
These basic differences make direct
comparison between jet engines and piston
engines difficult. Nominally the thrust output
of a jet engine remains the same, but the
amount of useful work it does can only be
determined with reference to the speed at which
it flies the aircraft to which it is fitted.
By combining the thrust of the jet engine
(which can be measured by direct means) with
the resulting speed of the engine-aeroplane
combination, the equivalent horse power of the
jet engine can be calculated.
If this is compared with the brake
horse power figures for piston engines, the
comparison is flattering to the piston engine,
since the B.H.P. figures takes no account of
propeller losses when the piston engine is set
to do the same job, i.e. produce thrust via a
propeller. For a rough comparison of
equivalent horse powers the effective horse
power of the piston engine can be taken as
three-quarters of the known brake horse
power--a figure acceptable in full scale
practice but still, probably, flattering to the
piston engine in model sizes.
With these facts in mind the
significance of the horse power curves for the
three Jetex engines tested can be appreciated.
Once the thrust output of the Jetex has been
determined (as the average of a number of test
runs), the equivalent horse power can be
calculated for different speeds.
If the Jetex "Scorpion" flies a model
at 30 m.p.h. for example, it is producing the
equivalent of 0.025 horse power for all the
time this speed is maintained. If it flies the
model at 60 m.p.h. the equivalent horse power
is 0.05 or somewhat higher than that likely to
be achieved by a 0.05 c.c. diesel piston
engine.
Actually, from the designer's point
of view, horse power figures for jet engines
are not particularly valuable. The basic
thrust figures are the ones which count most.
In the case of a Jetex unit, its rated thrust
determines the range of sizes of suitable
models, optimum model size for duration work
and also, together with the power weight ration
of the Jetex determines the limits for airframe
weight (i.e. total loading).
It was the original intention to make
up a suitable thrust testing rig to obtain
figures for the whole range of Jetex motors.
On a visit to the Wilmot Mansour factory to
discuss the test programme it was found,
however, that they already had a most efficient
and accurate thrust testing machine which they
agreed to loan to the Aeromodeller for
the series of tests. The machine was checked,
re-calibrated over the whole range of the scale
with static hanging weights as a double check
on accuracy and performed admirably throughout
the tests. Jetex users will no doubt be
interested to know that Wilmot Mansour do make
extensive use of this machine in checking
prototype and production Jetex units for
performance--a very real interest being shown
in continued development of the Jetex range,
despite the fact that they have a virtual
monopoly in this field. Bert Judge and Pete
Cock are just two of the particularly well
known aeromodellers on their staff.
The principle of operation of the
thrust testing machine is very simple. The
Jetex unit is clamped to a suitable carriage
suspended from knife edges. This carriage has
a free horizontal travel substantially parallel
with the base over the range of movement
required, The end of the carriage bears against
the vertical leg of an inverted "I" shaped
crank, pivoted in the Contra of the bar.
Pressure against this leg, as provided by the
thrust of the Jetex moving the carriage
forwards, produces a rotary movement of the "T"
shaped member which is translated into a
vertical "plunger" movement bearing down on top
of a flexible chamber (a squat, cylindrical
chamber with a rubber diaphragm top). This
chamber is filled with a suitable fluid and the
pressure transmitted to the flexible top forces
excess fluid out of the chamber up into a
vertical length of glass tube. The value of
the pressure applied is a function of the
height to which the liquid is raised in the
glass tube. The scale alongside the tube is
calibrated by means of hanging weights applied,
via suitable pulleys, to the carriage. A
suitable zero adjustment is fitted to vary the
initial pressure in the fluid capsule so that
the column of fluid can be adjusted to the zero
mark, as required, prior to any tests.
As for the test procedure itself,
this was basically straightforward--charging,
mounting and lighting the Jetex and then
recording thrust figures at regular intervals
over the duration of the run. Readings were
actually taken at two second intervals, an
assistant reading off the seconds from a
stopwatch whilst the operator studied the scale
and noted the reading of the liquid level at
each stated interval.
The resulting thrust figures plotted
on the graphs are the average of some fifteen
to twenty separate runs in each case. The
curves are also “smoothed,” in the
sense that the “wide scatter”
experienced, particularly over the first few
seconds of the run, has largely been ignored.
A pen recorder coupled to the thrust indicating
arm, for instance, would have produced a curve
of the same basic outline but with a wiggly,
rather than a smooth line.
The average of a large number of
readings was taken since separate runs with
identical Jetex units tend to be inconsistent.
There are, a variety of reasons for this,
connected with both the charges and the
condition of the Jetex itself. Despite all
efforts on the part of Imperial Chemical
Industries (the manufacturers of the solid fuel
charges) the charges themselves are far from
consistent. Some show a twenty-five per cent.
loss of power (thrust) as compared with,
perhaps, the next one out of the same box.
This is something Jetex users will have to
accept.
However, the condition of the Jetex
unit is something over which the operator has
some control. What are, apparently, small
factors can cause an appreciable loss of
power. If the wire core of the fuse is not
ejected completely from the nozzle when the
charge builds up to full thrust, for example,
the obstruction in the jet stream can result in
an appreciable loss of thrust. Leakage
between the end cap and body is also another
common source of thrust losses--due to improper
assembly or a burnt washer not seating
properly.
For maximum performance from any
Jetex motor careful and regular maintenance is
essential--frequent replacement of the gauze
holding the fuse against the charge (once every
third firing would appear good practice),
keeping the jet hole properly clean, careful
cleaning and assembly, and so on. In other
words, the instructions on cleaning and
maintenance given with each Jetex unit are
there to be followed--they are not put in to
persuade you to buy more spares and accessories
than you need.
Cost is, of course, one of the main
criticisms levelled against the Jetex unit. On
the face of it operating costs are high, but on
an overall basis they are not. A week-end's
flying with a diesel. powered model is likely
to work out more expensive on fuel alone,
flight for flight. The one great virtue or the
Jetex unit, by comparison, is then its virtual
indestructibility.
The two other "complaints" about
Jetex flying are that re-loading is a dirty
business and handling a hot motor to fit a new
charge can be a painful process! To the former
there is no answer, except that most model
engines are "dirty". Certainly the use of a
Jetex unit keeps the model cleaner than with a
diesel. And, of course, for the most
pleasurable operation of Jetex models two or
perhaps three separate motors, used
alternately, will allow each to cool down
adequately for comfortable handling between
flights. That, however, is making for
expensive flying although the Jetex being so
readily inter-changeable does encourage the
enthusiast to stick to one size of motor and
accumulate a stock of such units.
As to the individual units, the Jetex
350 is a “strong man's motor.” It
is an excellent prospect for duration flying,
both on account of its high average thrust and
the fact that the effective power run can be as
high as 36 seconds (with three charges).
Frequent assembly and dissembly of the five
strong spring clips holding the cap in place
is, however, a little hard on the hands! On
test, the "350" unit produced considerably
higher thrust figures than those claimed by the
manufacturers. Average thrust approached 4
ounces maintained over a period of about eight
or nine seconds. The initial build-up of
thrust is fairly slow, but there was no great
delay between the firing and thrust build-up of
the second and third charges. Each charge did,
however, produce a marked surge at the
beginning of the run and there was a slight
tendency for the average thrust to increase
with succeeding charges. Operating with one
charge only loaded in the bottom of the unit
produced an almost identical thrust run to that
achieved with the first charge when all three
were loaded. The marked variation between the
highest and lowest figures achieved over a
single run are noted on the graph and can be
attributed to variations in the fuel charges
themselves.
By comparison the "Jetex 200"
produced an appreciably higher average thrust
from the second charge on a two-charge run and
also the delay between the first charge
fizzling out and the second one cutting in
properly was most marked. This change-over
delay can be shortened by sandwiching a coil of
fuse between the two charges or slightly
hollowing out the lower charge and covering
with a layer of powdered charge before
inserting the final fuel pellet.
In the case of the "200" again the
thrust was appreciably higher than that
originally quoted for the unit-average thrust
exceeding 3 ounces for the second charge. For
duration contest work, therefore, where flight
time is computed as a ratio of total duration
to length of power run, loading a "200" with
two charges, firing in the normal way but not
releasing the model until the second charge has
built up its proper thrust is expensive, but
good practice. As a matter of interest loading
with a single charge and heating the whole unit
prior to firing produced a higher thrust figure
than from a single charge fired in the "cold"
state, but this practice is definitely not
recommended.
The Scorpion--the most powerful Jetex
unit in the range was the last to be tried in
this first series of tests and, apart from its
higher thrust output, the most outstanding
feature was the delightfully easy way in which
it could be assembled and dissembled. No
spring- loaded wire clips to struggle with-just
two spring rollers which snap in place with
delightful ease and a novel tubular mount for
the whole unit which makes it just as easy to
detach from the model, even when still quite
hot.
Another very interesting feature of
the "Scorpion" is the fact that the charge are
hollowed out at I the upper end. The coiled
fuse fits into this conical depression and the
gauze is similarly dished so that it maintains
good surface contact when pressed in place.
The resulting reduction in cross sectional area
of the charge during the initial burning period
eliminates the initial surge of thrust common
with the other plain cylindrical pellets. The
thrust, in other words; build up far more
uniformly, which is a particularly desirable
feature in any jet engine and gives effective
duration of some eight or nine seconds with a
nominal average thrust of just about 5 ounces.
This figure can be improved by the use of an
augmenter tube, supplied as standard equipment
with the Scorpion unit. Performance data
relative to the effect of augmenter tubes used
in conjunction with the range of Jetex units,
will form the subject of later
tests.
Part 2: The
Jetex 35, 50, 100 & Jetmaster (Dec
1953)
Concluding the series of thrust tests
on Jetex motors, comments on the performance
and handling characteristics of individual
units are given under separate headings. A
number of general observations can be made,
however, applicable to the whole range.
The same thrust-measuring apparatus
was used as in previous tests
(Aeromodeller, November, 1953), with
some slight modification of the
technique.
The question of consistency in Jetex
performance would appear of slightly greater
significance with the smaller units.
Inconsistency, largely, can be caused by one or
more of four major factors. There is the
variation in individual charges, due largely to
the fact that to produce these at a reasonably
low cost fairly generous performance tolerance
is necessary (actually this is of the order of
plus or minus five percent). The fuel has to
be prepared in batches, individually tested and
proved. Like many photographic solutions, just
preparing a mixture "to formula" is no
automatic guarantee of an acceptable
product.
The other three factors are to a
large extent, under the control of the Jetex
user. First-and this can have a most marked
influence-is the effect of air temperature and
humidity. Damp charges, like damp fireworks,
are relatively useless. Also on hot days (or
with warm charges on cold days) appreciably
higher thrust figures are realised than on
colder days. Exposed to a damp atmosphere
charges do, in fact, appear to attract moisture
and beads of "sweat" may actually appear on the
surface.
Ideally, therefore, charges should be
kept in a warm, dry place. On the flying field
this would indicate that charges are best kept
in the pocket, not in the model box and
certainly never laid out on damp grass. Drying
out of "suspect" charges, e.g. by gentle heat,
such as on top of a radiator, is
recommended.
The other major faults which can also
lead to inconsistency or poor performance are
"blow back", caused by improper sealing of the
case (e.g. a faulty washer, lack of adequate
spring tension, etc.) or a blocked or damaged
jet (e.g. wick core wire not ejected, or a
partially blocked jet through lack of
cleaning); both these faults tending to build
up pressure inside the case, aggravating the
tendency for the end cap to lift and leak).
Unless cleaned with the proper tool or correct
wire diameter, the jet hole may be enlarged,
when a permanent loss of thrust is almost
certain to result.
Another common fault with many Jetex
users is to find that the charge fails to fire,
due to improper loading, allowing the fuse to
fizzle out before the charge itself has
ignited. In this respect it is interesting to
note that throughout the whole series of these
tests with several dozen or more different
units and something like three hundred separate
runs, on only four occasions was ignition
failure experienced--three with the same
motor. In this particular case, almost
certainly the motor or the charge was
excessively damp.
No special, care was taken over
reloading each unit, except to note each time
that the gauze was pressed down securely and'
firmly against the charge and gauzes were
replaced, on average, every three runs.
The loss of thrust resulting from a
badly fitting end cap is most alarming. The
initial mechanical reaction on the charge
firing is for the end cap to blow open or lift,
reseating itself almost at once. Unless it
does re-seat itself with a perfect gas seal,
some of the expanding gases will inevitably
escape between the end cap and the casing, with
resulting loss of useful thrust. Replacement
of sealing washers, therefore, is a most
important feature of successful Jetex operation
whenever there is marked indication of
"blowing". In this respect, those units which
made replacement of the cap washer easy proved
more acceptable than older designs, from the
point of view of ease of maintenance.
A second, equally alarming feature of
Jetex units is the corrosive nature of the
gases generated when the charge is burnt.
Unfortunately this is something which is
inevitable. Rocket fuel is notoriously
corrosive, setting exacting specifications for
materials to stand up to the job. The
manufacturers investigated the properties of no
less than thirty different alloys before
adopting the present materials used-an
aluminium alloy with high hot strength and
retaining good corrosion resistance
properties. Where greater strength is
required, a stainless steel has proved the most
satisfactory material. The whole Scorpion
endplate, for example, is to be made of this
material.
The fact that all parts of a Jetex
are subject to corrosion means that if units
are left idle for some time, permanent damage
to the metals can result, since the corrosive
action is progressive all the while the metal
surfaces are contaminated with burnt charge.
This can only be avoided by a thorough cleaning
after use, dunking the whole unit in a bath of
paraffin after a day's flying is to be
recommended, which appears to arrest
corrosion. Units may then be cleaned down
later by scraping, etc., at leisure. Cleaning
in soapy water, followed by a rinse in clean
water and thorough drying is a normal
procedure. The unit then requires reassembling
with a new cap washer, lightly oiling the
ferrous metal parts which are, in fact, more
subject to corrosion than the non-ferrous
components.
These particular features have been
mentioned in some detail since their prevention
and cure lies entirely in the hands of the
operator--and to emphasise that although it has
no "working" or “moving" parts, a Jetex
engine needs proper maintenance, just like any
other engine.
The loss of thrust resulting from
failure of the igniter wick core to eject
itself can be overcome by a new method of
loading. Normally the first ex- plosive burst
as the charge fires (i.e. the one which
momentarily lifts the end cap) also blows out
the fuse core remaining in the jet hole. Here
it was noticeable that the units with a large
combustion space (i.e. a relatively large
"free", volume between the charge and the jet)
were more effective in blowing out the spent
wick (wire). A method of loading designed to
ensure positive ejection is to terminate the
fuse inside the loaded unit with a coil both
above and below the gauze. A short length of
fuse is then inserted from the out- side,
through the jet nozzle, to contact the main
fuse. This method is thoroughly to be
recommended, both for the fact that it does
ensure positive wick ejection and also because
it simplifies loading, particularly on units
with an extended end cap as in the 35, 50B, and
Jetmaster).
Jetex Atom 35
This is the smallest and lightest of
the Jetex units with a nominal or rated thrust
output of 3/8 to 1/2 ounce. It has one or two
different features compared with older Jetex
units.
The design is essentially a simple
one, which makes maintenance and loading easy.
The end cap has a tapered combustion chamber
leading to the actual jet nozzle (hole), the
external shape of the end cap making it
suitable for use with an augmenter tube.
Another particularly interesting
feature of the "35” is the hollowed
charge. Unlike the Scorpion the hollow end of
the charge is inserted first, and it matches up
with a dome-shaped bottom shield. The object
of this is to reduce the burning area towards
the end of the charge and thus prevent the
surge of thrust common with the smaller Jetex
units and normal solid cylindrical
charges.
On test this feature did appear
responsible for a reasonably flat thrust output
curve. Occasionally, however, charges did show
a momentary peak of power at the end of the
run, although this was the exception. The
characteristic thrust pattern is shown in the
graph, the maker's claim for thrust figures
being well substantiated, with an average
thrust approaching the half-ounce mark. It is
difficult to give true figures for the duration
of run since the thrust builds tip very slowly
at first and may take some ten seconds from
first lighting tile fuse to tile development of
full thrust. The effective run at rated
thrust is between 6 and 7 seconds, on
average.
Some eight "35's" were actually
tested during the series. A tendency to "blow"
on one or two would undoubtedly have been
improved by a slight increase in spring
tension to ensure more powerful re-seating on
the end cap after the initial burst. This is
something which the user can readily adjust,
himself and might well be attempted if signs of
leakage occur (indicated by dark stains on the
outside of the case). Check first, however,
that the fault is not the sealing washer.
Sometimes a washer will fail after the first
run. Others will last a large number of runs,
giving good sealing each time. The first run
is, in fact, probably the most critical, as far
as the sealing washer is concerned. The first
heating vulcanises the rubber content of the
impregnated asbestos washer and, virtually,
stabilizes it. Subsequent failure is then the
result of mechanical damage to the
washer.
The charges for the "35" were found
to be quite a tight fit in the case, calling
for adequate cleaning out each time to avoid
the fresh charge jamming. Some charges, too,
have small blobs or projections on their outer
surface, tending to make them slightly
oversize. These are readily rubbed off.
If a charge jams, about the only
thing to do is to carve it out with a knife,
taking care not to damage the soft metal of the
case. The charge can, also, be ignited with a
slow burning fuze and allowed to burn out,
although this may be only partially successful
in a damp atmosphere. In any case, this method
heats the case and there is a time delay before
re-loading until the case has cooled down
again.
Jetex 50 Units
Some dozen "50" units were tested A
in all comprising the new 50B, the original
(Standard) 50 and the export 50. Main
differences are in the shape and length of the
case. The standard 50 (which is to be dropped
from pro-duction) has a ribbed case. The
export 50 and 50B have nozzle-shaped end caps
to use with augmenter tubes, the 50B being
slightly longer. The idea in making the 50B
longer was to increase the " free" combustion
space to give better wick-ejection
properties.
All units use the same standard
charge and all give substantially the same
thrust figures. Average thrust is of the order
of 1/2 to 5/8 ounce, peaking to 7/8 ounce, or
even higher, at the end of the run. In other
respects, the export 50 and 50B are essentially
similar to the 35.
Jetex 100
The 100 retains its original form
with turned, instead of drawn case, and rather
elaborate triple spring; although these
probably give a higher sealing pressure, it is
far more troublesome to load and unload than
its modern counterparts.
Test figures indicated an average
thrust in excess of 1 ounce with an end surge
of up to I-1/2 to 1-3/4 ounce, with standard
fuel. Effective duration was of the order of
15 seconds, With Red Spot fuel average thrust
is increased to 1-1/4 ounce plus, with
effective duration cut to 12 seconds.
The 100 is actually being withdrawn
from production, in favour of the Jetmaster
which develops appreciably more thrust with the
same charge. It has, nevertheless, proved a
popular and useful unit over the past few years
and many thousands will undoubtedly continue in
service. All spares, etc., will continue to be
available.
Jetmaster
The Jetmaster features an extended
cap, designed expressly as a matching fit to an
augmenter tube. Particular care has been given
to the design and shape of the combustion
chamber with plenty of free space, and the
venturi section employed for the jet nozzle,
The unit is simpler than the 100 for loading,
etc., but features more parts for dissembly
when cleaning and calls for a special tool for
cleaning the jet nozzle, working from each end
in turn. The latter must be cleaned out after
each flight. If not cleaned, then there is a
very real danger of the fuse core jamming in
the nozzle and blocking the jet, instead of
being ejected. The best that can happen in
such cases is an almost complete "blow-back"
with little or no thrust. The worst--a split
casing.
The Jetmaster takes either standard
or Red Spot fuel, both of the same physical
dimensions but slightly different chemical
composition. A higher gas pressure, and higher
thrust, results from the latter, at the expense
of a decrease in duration. time (i.e. a higher
rate of burning).
Average thrust with Red Spot fuel was
consistently of the order of 1-7/8 ounce,
peaking to 2-1/4 ounces at the end of the run.
Effective duration was some 10 to 12 seconds.
With standard fuel average thrust was 1-3/8
ounces, peaking to 1-3/4 to 2 ounces.
Effective duration in this case was around 15
seconds.
Standard fuel will no longer be
available after present stocks are exhausted.
Red Spot, with its improved performance, will
then be the only fuel available for both the
100 and Jetmaster. Another point of interest
as regards fuels is that owners of old Jetex
units--or of old standard fuel-may find they
get lower thrust and higher duration figures
than those given by the test results. All
"standard" fuel--and this applies to all sizes
of fuel--has been of revised composition for
the past ten months or so giving higher thrust
and lower durations than previous "standard"
fuel.
Since the Jetmaster is undoubtedly
one of the most popular units to consider for
contest work, certain points must come in for
criticism-mainly the method of mounting.
Interesting as it may appear--and however
admirable an example of light production
engineering--the mount supplied for the
Jetmaster is virtually useless. It fulfills
the ideal of providing a simple clip-in mount,
but that is all. The unit Is barely secure and
there is no guarantee of obtaining a consistent
thrust line setting each time. This has been
apparent on the flying field where contest
modellers using the Jetmaster have employed
own-design.
Another point is that the "wick
injection” method of loading is the only
satisfactory method of loading the Jetmaster.
Fiddling an over-length piece of wick through
the inside of the combustion chamber and into
the jet venturi is too trying on one's
patience. Another point is that it would be
nice if some of the nine or more separate parts
forming the main end cap could be eliminated or
redesigned for greater ease of dissembly for
cleaning.
Some data on the effects of augmenter
tubes Jetex units will be published in an
abridged report next month.
Part 3: Jetex
Augmenter Tubes (Jan 1954)
Three sizes of Jetex augmenter tubes
are now available, supplied as standard
accessories for the 50B, Jetmaster and Scorpion
units. The 50 augmenter tube is made in three
parts, drawn from thin walled aluminium tubing,
individual lengths fitting together
telescopically. The bellshaped mount can be
fitted with one or two extension tubes, making
the total length of the augmenter tube 4 or 6
ins. respectively. The Jetmaster augmenter
tube consists of a bellmouth (made from two
pressings with a turned-over flange) and a 12
in. tube (also flanged), in 0.007 in.
aluminium. The Scorpion augmenter employs the
same bellmouth but an extension tube of only 41
ins. in length.
Basically an augmenter tube can be
considered to have two main purposes--to boost
the jet efflux (i.e., provide increased thrust)
and also to provide an efficient extension of
the tailpipe so that a Jetex unit can be
mounted amidships and the jet itself exhausted
from the rear of a fuselage. Thus, more
specifically, an augmenter tube makes it
possible to mount a Jetex unit in the fuselage
of a single-jet flying scale model with a true
scale or near-scale jet exit, rather than the
hitherto standard method of mounting the Jetex
in a trough under the fuselage.
As far as static tests were concerned
these had, of necessity, to be directed towards
measuring what effect the augmenter tube had on
the static thrust of the unit to which it was
fitted. Being static test figures, these do
not necessarily duplicate results which might
be obtained under actual flight conditions,
largely because there is no airflow through the
mount of the augmenter, other than the jet
efflux itself being fed into the centre of the
tube. Under flight conditions, provided an
ample, and smooth airflow is fed to the
bellmouth, quite possibly any beneficial
effects noticed on static tests may be
enhanced.
Summarising the tests, the Jetmaster
did show a remarkable increase in thrust with
augmenter tube added and properly positioned.
Highest thrust figures were obtained using the
shortest length of augmenter tube (Scorpion
size), but both short and long lengths gave
results above the nominal thrust figures for
the plain unit. Some lack of consistency is to
be noticed, however, which is most probably due
to the variation in fuel charges or the state
of the charges (e.g., damp charges giving low
thrust).
The 50B was another motor with which
slight increases in average thrust could be
detected when run with an augmenter tube.
Highest thrust figures resulted from using the
bellmouth only. Thrust gains with the
Scorpion, using an augmenter, were of a
proportionately lower order.
Both the 50B and the Jetmaster are,
of course, designed with shaped nozzles to
match the contours of the bellmouth. It would
appear that this is an essential feature if
marked thrust increases are to be achieved, A
Bluff trailing section in the bellmouth entry
(i.e., a "flat ended" Jetex unit) almost
certainly creates turbulence of an order
seriously to impair the efficiency of the
augmenter, hence no outstanding results are
likely to be achieved in such cases. The more
"flat plate" the trailing section of the Jetex
unit, too, the more critical the positioning of
the Jetex relative to the bellmouth entry
appeared to become. In the case of the
Jetmaster and 50B it appeared adequate that the
Jetex unit be lined up approximately parallel
with the tube and substantially central with
the longitudinal axis of the tube, the end cap
being in line with the leading edge of the
bellmouth.
Conclusions would appear to be that
the use of an augmenter tube as a thrust
booster should show favourable results with the
35 50B and Jetmaster and, to a lesser extent,
the Scorpion and other motors in the range.
For maximum effect a short augmenter tube
seemed consistently to give higher thrust
figures than any other arrangement and might be
considered as a useful feature in a
Jetmaster-powered duration model.
It is doubtful if the thrust
increases obtained with augmenters on the other
units is worthwhile from a duration design
point of view, particularly on account of the
fact that if this tube is mounted externally
and aligned with an offset motor (frequently
employed for trimming), glide trim may be upset
by the non-linear airflow through the
augmenter. Even aligned with the flight path,
augmenter drag may be quite high on the glide,
again affecting trim and glide
performance.
Using an augmenter tube to solve an
installation problem on a scale or near-scale
model, however, the designer can adopt the
arrangement with some confidence. Provided the
set-up is reasonably accurate he should
certainly get no loss of thrust, and most
probably a gain if a properly ducted entry is
associated with the location of the bellmouth.
This latter feature may be somewhat critical on
certain layouts.
Transposing the point of (free) exit
of a jet stream without loss of thrust is an
accomplishment of no mean order and for this
reason alone augmenter tubes are a welcome
innovation.
... ... 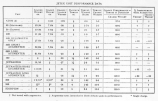
Click to see larger images
[Preceding is based upon articles
titled “Engine Analysis No. 15 (New
Series), by Ron Warring, in Aeromodeller
(Nov & Dec 1953, and Jan 1954), to which we
give credit.]
The
Sidewinder Design
From Flying Models magazine,
April-May 1960, p 21., to whom we give full
credit.
The
"Sidewinder" is an unusual approach to the high
power problem present on Jetex powered models.
A closer look at the pictures and plans will
reveal that the fuselage is off-center, and not
the side-mounted Jetex unit. Apart from that,
the "Sidewinder" is conventional in appearance
and construction.
After
several years of Jetex flying it became
apparent to us that for best results the Jetex
unit should be placed so that it is close to
both the center of resistance and center of
gravity. This was suggested by Ray Booth in an
article in the September 1958 issue of Flying
Models. This has been proven out as the plane
is rock steady under power and runs as if on
rails.
This
meant that the Jetex unit would be positioned
quite high on the fuselage and that the thrust
line would be off-center unless we built a
fancy fuselage around it. Competition models
must be simple and functional, and the fancy
fuselage went out the window. We then decided
to mount the fuselage off-center instead of the
jet. Using a tilted tail for turn in the glide
in previous models handled the power turn
nicely. Using an off-center thrust line now
would complicate matters. An added feature to
this off-center fuselage arrangement is that
the stabilizer assumes the proper tilt for a
nice glide circle.
The
original "Sidewinder" had an ultra-thin wing
which was discarded after several attempted
flights and after the present wing was built it
really began to perform. The only change after
that was a reduction in rudder area. It does
appear small but many test flights prove it
must be as is.
All the
important dimensions are shown on the plan to
ease the job of scaling them up. All wood used
is medium weight balsa unless specified
otherwise. Take care to keep the weight of the
finished model (including Jetex unit) between 2
to 2-1/4 oz.
Since
the fuselage is quite simple, we'll start with
the flying surfaces and then construct the
fuselage, while waiting for the cement on these
surfaces to dry.
Start
wing by cutting out all ribs from 1/32" sheet.
Stack all the ribs together for sanding and
notching, except the "A" ribs. The reason
being that it is an extremely difficult job to
line up all the spar notches between the
diagonal ribs "B" and the straight "A"
ones.
Now, pin
down the 1/8" sq. leading edge and the 1/32" x
3/8" tapered trailing edge. Place, but do not
pin, the 1/16" x 1/8" bottom spars down and
then cement all the "B" ribs down, working from
one tip toward the other, and pulling one rib
at a time from the stack. Doing this will line
up and space the bottom spars properly. Now
notch only the bottom of the "A" ribs for the
bottom spars and cement them in place. Now by
placing short lengths of 1/16" sq. strips in
the notches of the "B" ribs and extending them
over the "A" ribs you will see where to notch
them for 1/16" sq. spars.
Multi-spar wings are excellent for
light-weight models because of their high
strength-to-weight ratio, but care must be
taken to keep the spars straight. The above
mentioned procedure will accomplish the desired
results with the least effort. After the
cement has dried, block up the wing and cement
in the correct dihedral angles. Finally, give
the wing a good sanding.
The
stabilizer is made completely from strip stock
and is described on the plan. The leading
edge, trailing edge, and spar should be from
hard stock and the strips that make up the ribs
should be from very light, soft stock. Sand
the stabilizer thoroughly to a good airfoil as
shown on the plan.
As we
mentioned before, the fuselage is quite simple
and can be built while waiting for the cement
on the wing and stab to dry. Cut the fuselage
from a medium weight piece of 1/4" x 2” x
36" balsa. The weight for a piece of balsa
this size shouldn't exceed 1-1/4 oz. Cement
the basswood angle stiffeners in place next.
The best way to do this is to pin them in place
by crossing the pins over them and spacing them
at two to three inch intervals, and spot
cementing the angles to the fuselage with quick
drying cement.
When
dry, remove the pins, and run a bead of slower
drying cement on both sides of the angles. The
basswood angles are used in model railroad
building and should be available where such
supplies are sold. However, a very hard 1/8"
sq. cut diagonally as indicated on the plan,
may be used.
Cement
the hardwood engine mount in place at this
time. Now add the platforms, rudder, the
plywood dethermalizer stop, and the 1/8" dowels
for the wing hold down and the lower
dethermalizer hook.
It is
best to notch the fuselage for the wing
hold-down dowels and cement them in place
before the wing platform. Give the fuselage a
good sanding, rounding all corners, and build
up a skin of cement on the nose as indicated on
the plan. Apply at least two coats of sanding
sealer, after each coat, and then one thin coat
of color.
The wing
and stabilizer are now covered with Jap
tissue. Use a bright color for good
visibility. Spray with water to tighten and
then dope, using two or three thin coats. We
use two thin coats of nitrate dope and one coat
of Tuff fuel proofer. Naturally, you don't
need to fuel proof a Jetex model, but we find
it also serves another purpose. It keeps the
covering from going limp in humid climates. We
noticed this several years ago when attending a
meet at which the humidity was extremely high.
The covering on all our models sagged, except
that of the gas models which had been finished
with Tuff fuel proofer. Since then we have
applied one coat of Tuff to all of our models
just to prevent a reoccurrence of this
incident. It really works.
After
the stabilizer is covered and doped you can
cement the 1/16" plywood hold-down hook and
upper dethermalizer hook in the slot that has
been provided for them.
Assemble
the model now and align all the surfaces
properly. This is important! Then cement keys
to the wing and stabilizer to insure that the
model will be assembled correctly every time
and that the surfaces will not shift when in
flight. Now temporarily strap the Jetex motor
(unloaded) to the fuselage and shift fore and
aft until the model balances one inch in front
of the trailing edge of the wing. Mark this
location and then fasten the motor clip
permanently, taking care to see that it is
exactly on the thrust line.
With the
model still assembled, tie a length of thread
to a pin and then push the pin into the center
wing rib, from the top, at the center of
gravity location. Suspend the model by the
thread and add a small amount of weight to the
left wing tip until the model hangs level, when
viewed from the front. Cement the weights to
the wing, or remove a small section of covering
and cement them inside and then replace
covering. Check the model for warps and remove
them by steaming.
Flying
the "Sidewinder" is simple, especially since
warps have been removed and the model has been
balanced properly. The stabilizer has the
correct tilt (it is parallel to the inner right
wing panel) for a right hand glide circle.
Adjust only the stabilizer incidence, if
required, to produce a nice flat glide.
Now load
Jetex with one pellet, light up, and launch,
after the thrust has built up. Don't throw,
but shove slightly as though you are gliding
it. Watch for any sharp turning tendencies.
Correct them with rudder adjustments. Cut the
rudder free from the fuselage at the trailing
edge for about 1/4". This will allow you to
bend it slightly for adjustments.
At this
stage you should aim for a straight away climb
with no turn. Making the model turn now will
result in a vicious spiral dive under high
power. If all is well, proceed by adding more
pellets, until the model is flying with a full
charge. The final flight pattern should be as
follows. A straight away climb from the launch
for about 7-8 seconds, and then a slight turn
either right or left will develop as the thrust
increases. This will develop into a near
vertical climb, with a slight roll during the
final few seconds of thrust. A perfect roll
out into the glide follows.
A few
things to watch under high power. During the
last final kick of thrust the model is moving
very fast. Sometimes it will start to spiral
down. This is probably due to a bad warp
somewhere in the flying surfaces. If you can't
remove it, bend the rudder to make the model
turn against the warp. If the spiral still
persists the only alternative is to build a new
surface. If you can't see any warp, check to
see if the fuselage is bent. A bent fuselage
will throw the entire tall assembly out of
line.
Just
keep in mind that all your adjustments are
greatly magnified during that last final high
thrust kick and a poor adjustment could bring
your model back down at this crucial period,
instead of sending it sky high. Above all,
please follow the manufacturers instructions
for proper and trouble free operation of the
Jetex unit.
Jetex
Helicopters
Originally published in
Aeromodeller, Jan 1951, to whom we give
full credit
Though
photographs of working semi-scale helicopters
have often appeared in overseas magazines, full
credit for the first successful public
demonstration of realistic helicopter flight in
this country must go to pioneer F. G. Boreham
who lives at Waltham Chase, Southampton.
Aided
through his lengthy experiments by his friend
D. A. Smith, Mr. Boreham has spent many years
of study with rotating wing aircraft. He is a
Founder member of the Helicopter Association of
Great Britain; by profession an Aircraft
Inspector, and for most of his fifty years has
pursued the unorthodox phases of
aeromodelling. Small wonder then, that the
hard graft of trial and error should have
culminated in the magnificent display of stable
ascent and descent on the occasion of the 1950
Thurston Helicopter Trophy, Northern Heights
Gala. . . And what a pity this realistic
demonstration should have been limited to the
few fortunate viewers who happened to be on
that side of the field!
However,
Mr. Boreham's experiments have attracted the
attention of the Jetex manufacturers and
co-operation has produced a batch of models
suited to kit production, so that now the
pleasures of scale-like helicopter flight are
freely available, in commercial kits.
Mr.
Boreham has kindly supplied details of a simple
fixed blade 'copter for twin Jetex 50 power.
It is the very simplest form of model,
utilising the "beam power mounting" developed
to cure instability-one of the many
difficulties so prevalent in earlier designs.
This version should climb vertically for the
duration of its power run, but will not
auto-rotate in the “glide”' as
those with the hinged-blade system.
Design
Preceded
by rubber-driven experiments, Mr. Boreham's
twentieth model was the first to be fitted with
Jetex power units. With a rotor diameter of 24
inches, it had two “50” units
mounted at the extremity of the rotor blades
(referred to as the “Rotor
System”). Though it had fixed blades it
was capable of some ten seconds on each flight;
but the units were remounted "beam" fashion in
following models.
The
balance of the rotor blades is important,
otherwise the fuselage will oscillate badly and
the model will be erratic in flight. Similarly,
it should be remembered that both jet units
should be ignited at the same time to avoid out
of balance forces during the power run.
Though
safe and scale-like ascents were easily
accomplished by the earlier models, the
descents were not always as desired and usually
far too rapid. Various ideas were tried in an
effort to obtain auto-rotation, and eventually
a full-size practice, known as “delta
3” was found to be the answer.
Briefly,
this may be interpreted as a method of blade
hinging, so that, when the blade flaps tip (or
increases its dihedral angle), it also
decreased the angle of incidence on the blade.
Similarly, the incidence increases as the blade
flaps down. All the later models incorporate
this system, which has reduced the rate of
descent so effectively with autorotation, that
experiment No. 45, of 36 inches diameter, with
twin Jetex 100 units, constantly averages
around the 60 seconds mark.
Twin
100 Model
Rotary
wing enthusiasts who might wish to try their
own hand at helicopter design will find Mr.
Boreham's specifications for a twin
“100” model invaluable. The blade
diameter should be 34 inches. Two blades, each
14 x 2 inches tapering to 1 inch wide at the
tips are made from 1/8 in. sheet balsa, sanded
to an airfoil section of Clark Y type. The
Jetex 100 units are mounted on a 1-1/16 inch
ply beam, 15 inches long and 1 inch wide, which
is glued and bound at 90° to a 6 x 1 x 1/4
inch centre section. This carries an aluminium
tube to act as the hub.
The
blades are then hinged to the centre section
beam, using 20 s.w.g. wire hinges, suitably
bound with thread and glued. The delta angle
of the hinge is 35° to the blade centre
line, and the maximum pitch setting with the
blades horizontal is 15°. Total weight,
ready for flight, should be around 4-1/2
ounces.
A 10
inch stabilising fuselage, 2 inches deep at the
front and tapering to 1 inch at the rear, with
a 4-1/2 x 1 x I in. nacelle in front of the
rotor hub, will provide weathercock stability
and not turn in flight. The undercarriage can
be a simple wire axle with 5/8 inch wheels
spaced 5 inches apart.
It was a
model built to the above data that made the
outstanding show at Langley, and proved that
realistic helicopter flight is no longer a pipe
dream.
The preceding article was originally
in Aeromodeller, January 1951. No
author is named.
Jetex
Helicopters
.... 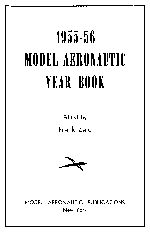
This article originally appeared in
the Zaic Yearbook 1955-56, by Parnell
Schoenky. Click images to see full size
graphics (two) pages of the article.
Getting the Most Out of Your
Jetex
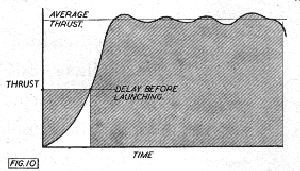
If
you have any Jetex articles or
information that we might post here,
please let us know.
|
|